This article explains how lap joint flanges works, why we choose them and other common alternatives available in industry.
Flanges are used in piping systems to connect pipes to equipment and other piping as well as instrumentation components, special items etc. They provide added flexibility during assembly, disassembly and maintenance of piping systems.
Lap joint flanges are one of the popular choice of flange type used in piping systems as well as ducting systems,
It is essential to understand how a lap joint flange works and various design differences in them, to ensure a safe, reliable operation as well cost effectiveness.
In this article, we are going to understand how lap joint flange work, which are the various options available when buying a lap joint flange and key considerations to keep in mind when buying them.
What is a lap joint flange
Lap joint flanges are also known by other names such as:
- Van Stone Flanges
- Loose Ring Flanges
- Loose Hubbed Flanges
- Back Up Flanges
Lap joint flange consists of two parts namely
- Lap Joint Stub End : This is butt welded to pipe.
- Backing Lap Joint Flange : It slides on the stub end before stub is welded to pipe.
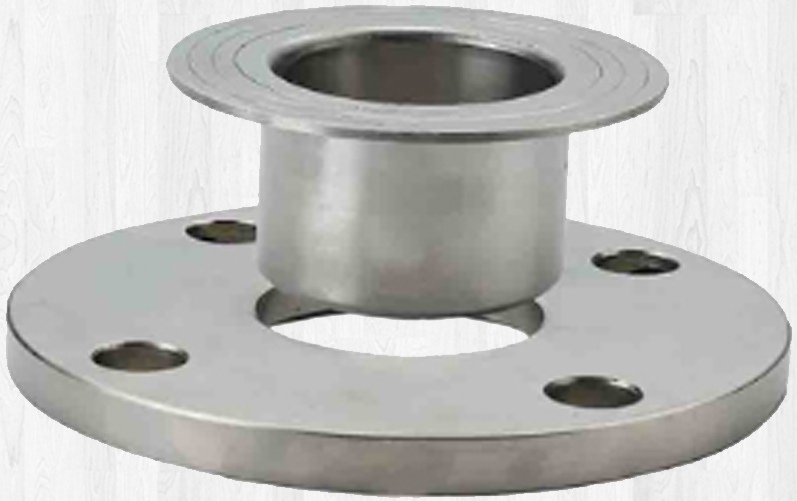
Lap joint flanges are very similar to Slip On Flanges. But Lap joint flanges include a radius at the intersection of the flange face and the bore to accommodate the flanged portion of the Lap Joint Stub End making it only compatible to Lap Joint Stub Ends.
Materials for Lap Joint flanges and Lap Joint Stub Ends vary and may even differ in a single implementation to allow for greater cost flexibility.
Materials typically used for Lap Joint flanges include a range of stainless steel, carbon steel and other alloy materials.
Lap joint flanges are are available in standard dimensions like other flange types. It makes them easy to integrate into existing piping systems or use alongside other piping components like valves, equipment, etc.
Stub Ends also match both pipe material and wall schedule to maintain both inside and outside diameters of your piping system. This style is typically used in engineered piping systems with critical wall thickness requirements.
Lengths
Stub Ends are also available in two different lengths.
- MSS or Short lengths
- ASA or Long lengths
Face Finishes
Stub ends are available in different face finishes. Example is Serrated finish which can help to increase gasket adherence.
Difference between Lap Joint Flanges and Rolled Angle Rings.
Rolled Angle Rings which are also known as Vanstone Rings or Vanstone Rolled Angle Rings have similar benefits to Lap Joint Stub Ends with similar designs and installation requirements.
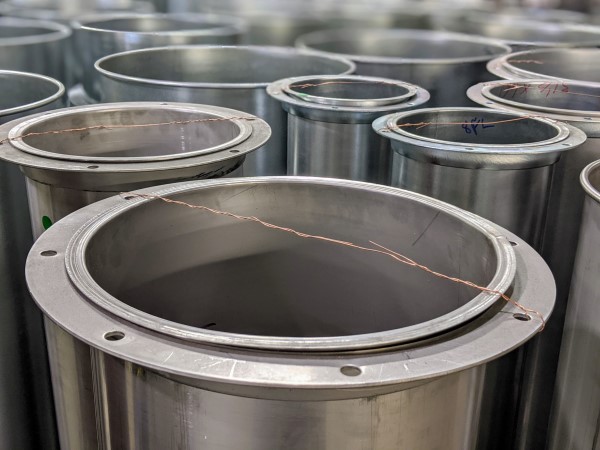
Rolled Angle Rings are not standard fittings. There are subtle differences that makes one preferable over the other in most cases.
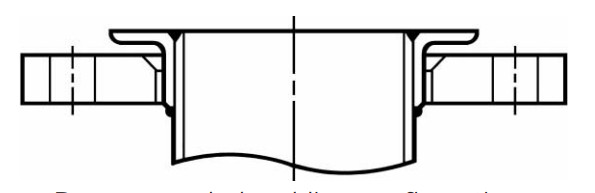
Just like Lap Joint flanges, the two-part design means the rolled angle ring and backing flange can be comprised of different materials for added flexibility and cost optimization potential.
Example Rolled Angle Ring : 316/L SS rolled angle ring with a Carbon Steel, Galvanized backing flange.
The backing flange is also free to rotate on the pipe, allowing for easier alignment.
Unlike Lap Joint flanges, rolled angle rings are available in two different installation configurations:
-
Butt-Weld
-
Slip-On
Butt-Weld Rolled Angle Rings install similarly to Lap Joint Stub Ends, requiring welding to the end of the pipe and matching of the inner diameter of the pipe or fitting in use. Slip-On Rolled Angle Rings slide over the pipe, attaching to the outside of the pipe wall instead of the end.
Rolled Angle Rings are also not manufactured to match the thickness of the pipe or fitting they are connected to. Mostly they are made from 11 gauge Angle Iron. Larger pipe sizes might use 7 gauge Angle Iron.
Smaller rings are made from piece of plate cut to specific inner and outer dimeters, using hydraulic press. These are called pressed angle rings or I.D. Pressed Vanstone Rings. They are seamless ring and easy to produce and replicate. However, having the exact 90-degree angles of Rolled Angle Rings is difficult using hydraulic presses.
Advantages and Disadvantages of Lap Joint Flanges and Rolled Angle Rings.
After knowing how these popular flange types work, we will discuss why you will like to use them in your piping systems.
Disadvantages
The biggest limitation to lap joint flange usage is pressure ratings.
Similar to slip on flange, Lap joint flanges cannot be used in high pressure applications, It is necessary to consult piping materials engineer to ascertain viability of lap joint flanges in certain high pressure applications. Weld neck flanges are normally used in high pressure applications.
Advantages
- With lap joint flanges, we can use different materials for the Backing flange than the Stub End or Angle Ring. It means you can use the piping material compatible with the fluid passing through the pipe for the stub end and can use more affordable or desirable materials for rotating flange which do not interact with the process fluid.
- The second advantage is the ability to realign and rotate the flange freely to ensure proper connection with valves and other flanged components of piping systems. It greatly speeds up maintenance processes in systems that require frequent maintenance.
- Lap joint flanges do not require filet welds on the plates. This fact decreases installation times and provide further upfront cost savings.
- In high corrosion and high erosion processes, piping may have to replaced frequently. In such cases, only stub end portion of this flange is needed to be replaced. The backing flange can be reused saving cost of piping replacement.