ASME Standard B16.11 provides dimensions and requirements for Socket weld Fittings of sizes 1/8″ and upto 4″. But in most piping material specifications for process plants, only 1/2″ to 11/2″ size socket weld fittings are used. These fittings are made with forging process. Socket weld fittings are available in ratings 300#, 600# and 900#. Reducing fittings have the same center-to-end, center-to-bottom of socket, band diameter, and outside diameters as the uniform size fitting corresponding to the largest size end connection of the reducing fitting.
Tags : #Piping_Engineering #Piping_Fittings #Socket_Weld_Fittings.
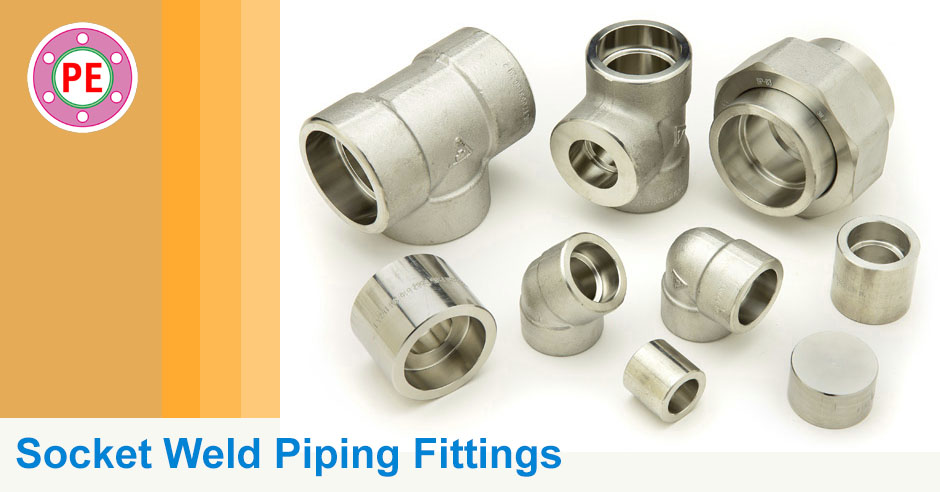
Dimensional Standards
- ASME B16.11 : Forged fittings, Socket welding and threaded.
- MSS-SP-79 : Socket Welding Reducing Insert
- MSS-SP-83 : Steel Pipe Unions, Socket welding and threaded.
- MSS-SP-95 : Swaged Nipples and Bull Plug.
Available Fittings
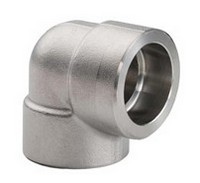
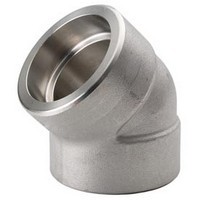
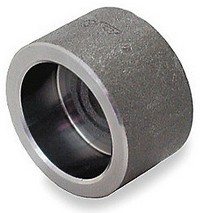
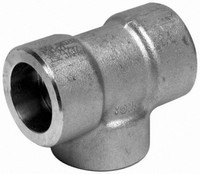
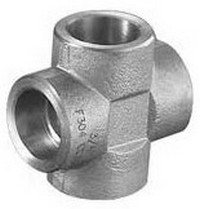
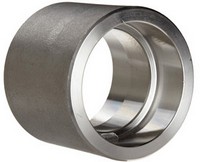
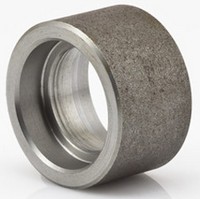
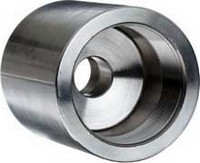
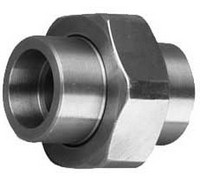
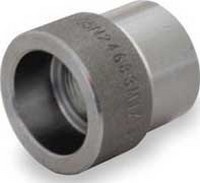
Materials of Construction
These fittings are forged fittings. So Materials of Construction are as follows.
- A105 : Standard Specification for Carbon Steel Forgings for Piping Applications.
- A181 : Standard Specification for Carbon Steel Forgings, for General-Purpose Piping.
- A182 : Standard Specification for Forged or Rolled Alloy and Stainless Steel Pipe Flanges, Forged Fittings, and Valves and Parts for High-Temperature Service.
- A350 : Standard Specification for Carbon and Low-Alloy Steel Forgings, Requiring Notch Toughness Testing for Piping Components.
Advantages of Socket Weld Fittings
- They are easier to use on small-size pipelines and ends of the pipes need not be bevelled since the pipe end slips into the socket of the joint.
- With socket welded fittings, there is no danger of the weld protrusion into the pipeline and restricting flow or creating turbulence.
- No tack welding is necessary for alignment since joint and the pipe are self-aligning.
- It can be used in place of threaded fittings, therefore, reducing the likelihood of leaks, which usually accompany the use of threaded fittings.
- It is less expensive and easier to construct than other welded systems. Joints will not leak when properly made.
Disadvantages of Socket Weld Fittings
- With socket weld fittings, there is a possibility of a mismatch inside the fitting where improperly aligned or mated parts may create a recess where corrosion could start.
- The 1/16 inch recess in joint for thermal expansion pockets liquid and also can cause corrosion, is case of highly corrosive liquids.
- Not used in Hydrogen Service. (All fittings are Buttwelding including small bore for hydrogen service).
- Use not permitted by ANSI B31.1 if severe vibration or crevice corrosion is anticipated.
Applications of Socket Weld Fittings
- For lines conveying flammable, toxic or expensive material, where no leakage can be permitted.
- For steam: 300 to 600 PSI, and sometimes 150 PSI steam.
Fittings Classes
Ratings for Socket Welded Fittings are Class 3000, 6000 and 9000.
Choice of Class depends on thickness schedule of pipe, as given in ASME B16.11. Socket welded : 3000:Sch 80 and XS, 6000: Sch 160, 9000:XXS
Sample Piping Material Specification
Elements : 45 Degree elbow, 90 Degree elbow, Equal Tee, Reducing Tee, Caps, Full Coupling, Reducing Coupling
- Carbon Steel : ASTM A105. Galvanised, NIC, HIC as per spec.
- Stainless Steel : ASTM A182 F304L
- Class : SW : 3000:Sch 80 and XS, 6000: Sch 160, 9000:XXS
- Ends : Socket Weld Ends, Threaded Female Ends, Dim Standard : ASME B16.11
Elements : Concentric Swage, Eccentric Swage
- Material : CS : Made from seamless pipe ASTM A234 Gr. WPB
- Material : SS : Made from seamless pipe ASTM A403 Gr. WP304LS
- Ends : Both Ends Plain, Bevelled larger end-Plain Small End (if large size 2” and above).
Elements : Reducer Insert
- Material : CS : ASTM A105,
- Class : 3000,
- Ends : Socket Weld Ends,
- Dim Standard : MSS-SP-79