Plate exchangers, shown below, are generally used in low-pressure, low temperature applications and are made up of end covers, carrying bars, inlet and outlet nozzles, plates and gaskets.
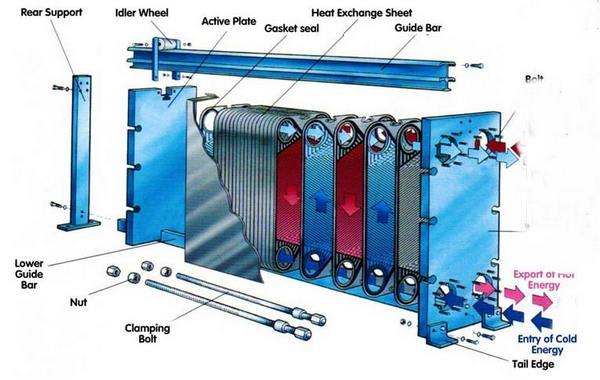
The exchanger plates have spacing between them for liquid flow. A gasket, set into channels on the periphery of each plate, directs and contains the liquid flow distribution.
Ports for inlet and outlet of both hot and cold liquids are stamped into the corners of each plate. When aligned, they form four distribution headers through the plate pack. Distribution of hot and cold liquids to alternate plate flow channels is achieved by the gasketing pattern around each port.
When the liquid is intended to flow through to the next plate, the gasket is left intact around the port. Alignment is achieved by top and bottom carrying bars and slots in each plate. When completely assembled, the plate pack and gaskets are compressed by bolts between two covers.
Support is provided by the fixed end cover and carrying bar. The plate exchangers requires less installation and servicing space then do shell and tube arrangements of equivalent surface.
Plate Heat Exchanger Location and Support
Plate heat exchangers can operate in series or parallel but because of their configuration and maintenance requirements, it is preferable to position them as single items.
Space is provided for control and operator access, with enough room to remove the individual plates.
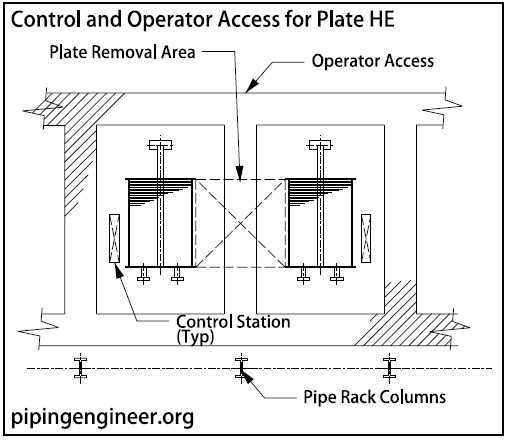
Plate Heat Exchanger Piping
Piping is positioned to allow the opening of covers and removal of plates. Controls are located at the front and on one side for the plate exchangers. Piping is elevated similar to that for shell and tube heat exchangers.
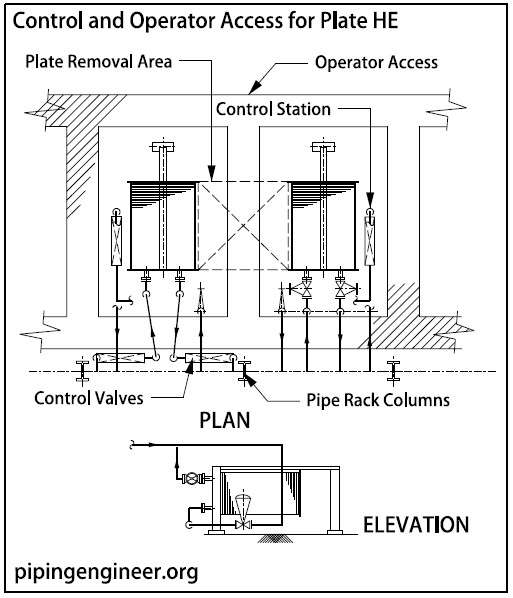
Plate Heat Exchanger Maintenance
Internal servicing at plate exchangers can be done manually. Following video shows cleaning of plate heat exchanger using dry ice blasting.